Advancement in Light Weight Aluminum Casting: Cutting-Edge Techniques for Modern Designers
What genuinely sets these developments apart are the lasting light weight aluminum alloys being established and the high-pressure die casting techniques that are revolutionizing the industry. Join us as we discover the center of aluminum casting innovation, where modern technology satisfies creativity to redefine what is feasible in the world of metal spreading.
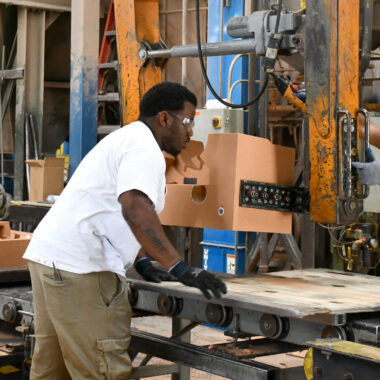
Advanced 3D Printing Methods
Making use of advanced additive manufacturing procedures, advanced 3D printing methods have actually changed the production of elaborate and personalized light weight aluminum parts. By employing high-precision printers that can work with light weight aluminum powders or filaments, suppliers can create complex geometries and designs that were previously unattainable with standard production approaches.
One of the essential advantages of sophisticated 3D printing in aluminum element production is the capability to accomplish light-weight yet long lasting frameworks. This is especially valuable in sectors such as aerospace and auto, where weight decrease is critical for boosting fuel efficiency and overall efficiency. In addition, the modification alternatives supplied by 3D printing permit for the production of unique and tailored components that meet certain demands, causing enhanced functionality and efficiency.
Moreover, the effectiveness of the 3D printing process minimizes product waste and lowers the general production time, making it an affordable option for manufacturing light weight aluminum components. As technology remains to advance, the capacities of 3D printing in aluminum production are expected to increase, using even greater opportunities for advancement in various industries.
Computer-Aided Layout Technologies
With the improvements in advanced 3D printing strategies for aluminum parts, the combination of Computer-Aided Design (CAD) software has actually ended up being increasingly crucial in driving development and efficiency in the manufacturing procedure. CAD advancements have revolutionized the method designers and engineers develop aluminum spreading molds by using precise electronic modeling abilities. These software program tools permit for the creation of complex layouts and simulations that enhance the spreading process, causing better parts.
One of the crucial advantages of CAD in aluminum casting is the ability to find potential problems early in the style stage, reducing expensive mistakes and revamp during manufacturing. By simulating the casting procedure basically, designers can evaluate aspects such as cooling down prices, material circulation, and architectural honesty before a physical mold is created. This positive technique not just conserves time and sources yet also makes sure that the last light weight aluminum parts fulfill the preferred requirements.
Moreover, CAD software allows quick models and modifications to styles, helping with fast prototyping and personalization to satisfy certain needs. By leveraging CAD technologies in light weight aluminum casting, makers can enhance their procedures, enhance product high quality, and remain at the leading edge of development in the industry.
High-Pressure Pass Away Casting Techniques
High-pressure die casting methods are widely recognized for their efficiency and accuracy in generating complex aluminum parts. By making use of high stress to require molten light weight aluminum right into complex molds at fast speeds, this technique permits for the production of dimensionally exact and thorough parts. One of the essential benefits of high-pressure die spreading is its capability to produce components with thin walls and great details, making it perfect for applications where light-weight yet solid components are essential.
The Read Full Report process starts with the preparation of the die, which is typically made from solidified device steel and consists of 2 halves that create the wanted component shape. The molten aluminum is then infused into the die tooth cavity under high stress, guaranteeing that the product fills up all the intricate features of the mold and mildew. As soon as the light weight aluminum strengthens, the die opens up, revealing the completed component prepared for any kind of required post-processing.
High-pressure die casting is frequently used in different sectors, including automobile, aerospace, and electronics, where high-volume manufacturing of complex light weight aluminum parts is required. casting aluminum illinois. Its capability to provide limited resistances, excellent surface finishes, and cost-efficient production makes it a preferred option for contemporary makers intending to introduce in light weight aluminum casting methods
Lasting Light Weight Aluminum Alloys Growth

One method to sustainable light weight aluminum alloy advancement entails incorporating recycled light weight aluminum content into the alloy make-up. By utilizing recycled light weight aluminum, suppliers can minimize power consumption and greenhouse gas discharges connected with main light weight aluminum manufacturing. Furthermore, reusing light weight aluminum aids divert waste from land fills, contributing to a more round economic situation.
Additionally, scientists are discovering new alloying elements and handling methods to improve the sustainability of aluminum alloys. By maximizing alloy structures and making procedures, it is possible to boost the recyclability, toughness, and total environmental performance of aluminum products.
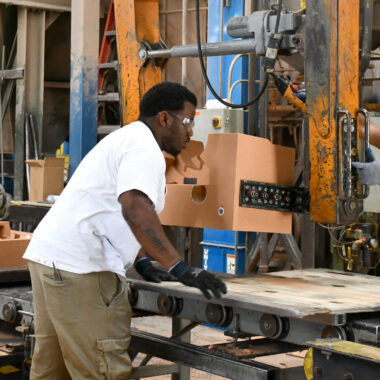
Automation and Robotics Combination
In the world of lasting aluminum alloys development, the assimilation of automation and robotics is reinventing manufacturing procedures, paving the way for raised effectiveness and accuracy in manufacturing. Automation and robotics are improving traditional spreading techniques, supplying various advantages to designers in the aluminum market. By incorporating automation right into the casting procedure, repetitive jobs that were once labor-intensive can currently be efficiently managed by robotic systems, reducing the threat of human error and boosting overall efficiency.
Automated systems can work around the clock, making certain a constant manufacturing cycle that reduces downtime and makes best use of result. Robotics assimilation enables complex molds and detailed designs to be generated with unrivaled accuracy, satisfying the needs of modern creators for top quality aluminum elements. The usage of automation in casting operations promotes a safer working atmosphere by lessening the direct exposure of employees to dangerous problems.
Verdict
Advanced 3D printing strategies, computer-aided layout advancements, high-pressure die spreading techniques, sustainable aluminum alloys development, and automation and robotics integration have all added to the innovation of the casting process. The future of light weight aluminum spreading is brilliant with continuous innovation and technical improvements.
What really sets these technologies apart are the lasting aluminum alloys being developed and the high-pressure die casting strategies that read here are transforming the pop over to this web-site industry. Join us as we discover the leading edge of light weight aluminum spreading innovation, where modern technology satisfies creative thinking to redefine what is possible in the globe of metal spreading.
One method to sustainable light weight aluminum alloy development includes incorporating recycled light weight aluminum material into the alloy structure - casting aluminum illinois. By utilizing recycled light weight aluminum, manufacturers can minimize energy usage and greenhouse gas emissions connected with key aluminum production. Advanced 3D printing methods, computer-aided style innovations, high-pressure die spreading methods, sustainable light weight aluminum alloys development, and automation and robotics assimilation have all contributed to the innovation of the casting process